- Home
- News
- Enhanced Efficiency and Precision: Discover the Benefits of Single Pallet Horizontal Machining Center
Enhanced Efficiency and Precision: Discover the Benefits of Single Pallet Horizontal Machining Center
By:Admin
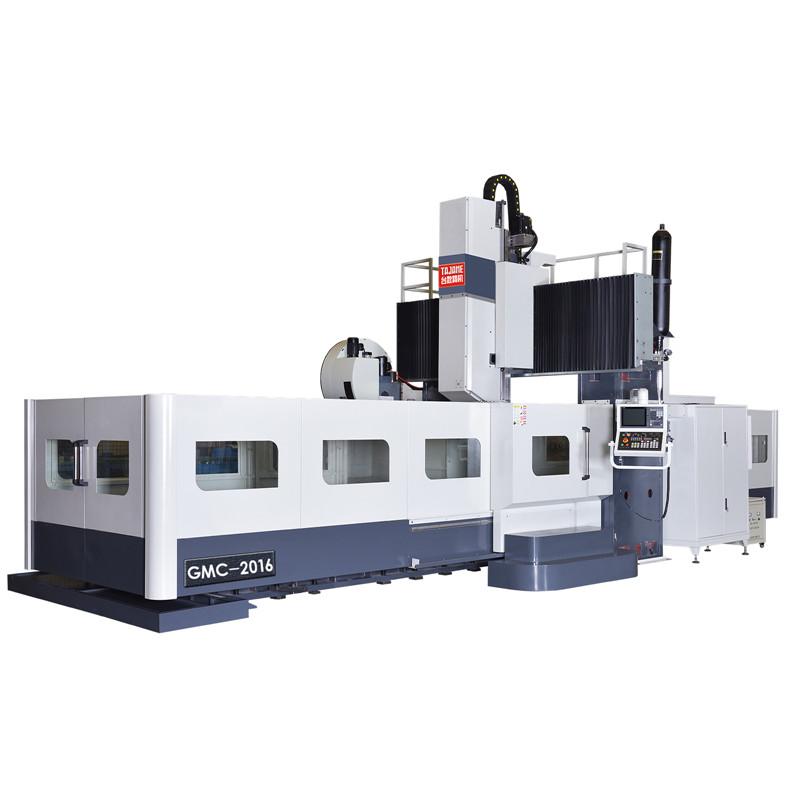
Introduction
In an exciting development for the manufacturing industry, {Company Name}, a renowned leader in precision engineering solutions, has recently announced the introduction of a highly advanced Single Pallet Horizontal Machining Center. This cutting-edge machinery showcases the company's commitment to constant innovation and its determination to stay ahead of the competition. With this new addition, {Company Name} has significantly bolstered its manufacturing capabilities, enabling enhanced productivity, increased efficiency, and unparalleled precision.
Unveiling the Single Pallet Horizontal Machining Center
The Single Pallet Horizontal Machining Center, designed and developed by {Company Name}'s team of dedicated engineers, represents a leap forward in CNC machining technology. This state-of-the-art equipment is equipped with advanced features that revolutionize production processes, making it an invaluable asset for businesses across various industries.
Features and Advantages
1. High Precision
The Single Pallet Horizontal Machining Center boasts exceptional accuracy, ensuring precise cuts and superior surface finishing. The incorporation of advanced motion control algorithms guarantees a seamless operation, delivering consistently superior results for even the most intricate and complex parts.
2. Enhanced Productivity
With its high-speed machining capabilities, this new machining center drastically reduces production time and enhances efficiency. The combination of rapid tool change systems, high-speed spindles, and advanced automation features allows {Company Name} to complete manufacturing tasks in record time, meeting tight deadlines while maintaining superior quality.
3. Versatility and Flexibility
{Company Name}'s Single Pallet Horizontal Machining Center offers unparalleled versatility, accommodating a wide range of materials, dimensions, and complex geometries. This allows businesses to take on a multitude of projects, streamlining their operations and maximizing their manufacturing potential.
4. Improved Safety Measures
Ensuring the safety of operators and personnel is a top priority for {Company Name}. The Single Pallet Horizontal Machining Center incorporates cutting-edge safety features, such as automatic tool detection and high-precision collision detection systems, guaranteeing a safe and secure working environment.
Implications for the Manufacturing Industry
The introduction of this advanced machinery marks a significant milestone for {Company Name} and the manufacturing industry as a whole. The Single Pallet Horizontal Machining Center offers an opportunity for businesses to enhance their productivity, reduce production costs, and maintain the highest standards of craftsmanship.
Additionally, {Company Name}'s commitment to innovation heralds a new era of possibilities for the manufacturing industry, encouraging others to follow suit and invest in cutting-edge technology to gain a competitive edge.
Future Prospects and Commitment to Sustainability
Despite its already impressive capabilities, {Company Name} remains dedicated to the continuous improvement of its precision engineering solutions. Research and development efforts are focused on optimizing the current Single Pallet Horizontal Machining Center while exploring sustainable manufacturing practices to minimize environmental impact.
Conclusion
{Company Name}'s introduction of the Single Pallet Horizontal Machining Center signifies an important milestone for both the company and the manufacturing industry. This highly advanced machinery embodies a combination of precision, versatility, and efficiency that will revolutionize production processes for businesses across various sectors. By leveraging this state-of-the-art technology, {Company Name} has solidified its position as an industry leader and remains committed to reshaping the future of precision engineering.
Company News & Blog
Discover the Latest Advancements in Machining Centers: Your Ultimate Guide
Title: Revolutionary Machining Center Unveiled: A Game-Changer in Industrial PrecisionIntroduction:In a groundbreaking move, a leading engineering solutions provider has unveiled its latest innovation, a state-of-the-art machining center that is set to redefine precision and efficiency in the industrial sector. With a commitment to technological advancement and customer satisfaction, the company has developed this cutting-edge solution to meet the evolving needs of the manufacturing industry. This article explores the features and potential impact of this remarkable machining center on various sectors of the economy.Unleashing Unparalleled Precision:The new machining center stands out for its exceptional precision, enabling manufacturers to produce intricate parts and components with unparalleled accuracy. Equipped with advanced computer numerical control (CNC) technology, the machining center offers high-speed machining capabilities that significantly reduce production time while guaranteeing precision within microns. This feature is poised to transform industries such as aerospace, automotive, and medical, where intricate details and precise measurements are critical.State-of-the-Art Automation:Automation has become an integral part of industrial processes, and the new machining center takes it to a whole new level. The incorporation of robotic arms and machine vision systems streamlines operations by automating material handling, tool changes, and quality control. This automation not only expedites production but also minimizes the risk of human error, ensuring consistent quality and reducing costs associated with manual labor.Enhanced Efficiency and Productivity:With optimized tooling and innovative cutting strategies, the new machining center significantly boosts efficiency and productivity in manufacturing processes. Its multi-axis capabilities and simultaneous machining options allow for simultaneous operations, reducing setup time and increasing throughput. This enhanced productivity directly translates to cost savings and enables manufacturers to meet growing demands efficiently.Seamless Integration with Industry 4.0:In an era of digitalization, the new machining center is designed to seamlessly integrate with the principles of Industry 4.0. With built-in sensors and connectivity features, it enables real-time monitoring, predictive maintenance, and data-driven decision-making. This integration empowers manufacturers to embrace the concept of smart factories and optimize their operations for maximum efficiency, leading to reduced downtime and improved overall performance.Commitment to Sustainability:The company's commitment to responsible manufacturing and environmental sustainability is apparent in the design and functionalities of the machining center. By incorporating energy-efficient components and minimizing material waste through advanced cutting strategies, this solution champions sustainability without compromising on performance. It aligns with global efforts to reduce the carbon footprint of industries and underscores the company's dedication to a greener future.Empowering Skilled Workforce:While automation reduces dependency on manual labor, the new machining center seeks to empower the skilled workforce by offering comprehensive training and support programs. The company recognizes the importance of human expertise in leveraging the full potential of this advanced technology. By providing training on programming, maintenance, and troubleshooting, they are ensuring that individuals adapt seamlessly to the evolving industry landscape.Expanding Market Opportunities:The unrivaled precision and versatility of the new machining center open doors to countless market opportunities. Its ability to produce intricate, complex, and high-performance parts makes it ideal for industries such as aerospace, automotive, electronics, and medical devices. It allows manufacturers to explore new avenues, enhance product offerings, and gain a competitive edge in an increasingly demanding market.Conclusion:The unveiling of this revolutionary machining center marks a significant step forward in the evolution of industrial precision and productivity. With its exceptional precision, state-of-the-art automation, seamless integration with Industry 4.0, commitment to sustainability, and focus on empowering the skilled workforce, this innovation is set to revolutionize manufacturing processes across various sectors. As the industry embraces this game-changing technology, it is poised to witness increased efficiency, reduced costs, and enhanced product quality, paving the way for a brighter and more prosperous future.
Exploring the Advantages of a Rotary Table Horizontal Boring Mill
Title: Innovative Horizontal Boring Mill with Rotary Table Enhances Precision and EfficiencyIntroduction:In today's ever-evolving landscape of manufacturing and industrial solutions, companies are continuously seeking innovative machinery that maximizes precision, efficiency, and productivity. Addressing these demands, an industry-leading company has introduced its highly advanced Horizontal Boring Mill with Rotary Table—an engineering marvel that redefines machining capabilities and sets new standards for the manufacturing sector.Context:The Horizontal Boring Mill with Rotary Table, developed by an industry pioneer, represents a significant breakthrough in machining technology. With its cutting-edge features and wide-ranging applications, this state-of-the-art equipment promises to revolutionize various sectors, including aerospace, automotive, energy, and beyond.Main Body:1. Precision Engineering at its Finest: The Horizontal Boring Mill with Rotary Table stands out for its exceptional precision and accuracy. Equipped with advanced CNC controls and integrated measurement systems, this revolutionary machine ensures that every component passes the most stringent quality standards. Its meticulous drilling, milling, and boring capabilities guarantee optimal fit and tolerance, resulting in superior end products.2. Advanced Features Enhancing Efficiency:The incorporation of innovative features in the Horizontal Boring Mill with Rotary Table translates into enhanced productivity and efficiency for industrial operations. Equipped with a robust rotary table, a wide range of multi-axis machining operations can be accomplished in a single setup, reducing production time and maximizing output. The machine's high-speed spindle motor enables rapid cutting while maintaining accuracy, further improving efficiency.3. Versatile Applications:With its adaptability and versatility, the Horizontal Boring Mill with Rotary Table caters to a variety of manufacturing needs. From producing complex components for the aerospace industry to manufacturing large-scale automotive parts, this machine is designed to handle a diverse range of projects effectively. Furthermore, its ability to accommodate different materials, including steel, aluminum, and composites, grants companies unmatched flexibility.4. Safety and Ergonomics:While pushing the boundaries of machining capabilities, the Horizontal Boring Mill with Rotary Table also prioritizes operator safety. Incorporating state-of-the-art safety systems ensures a secure working environment for the machine's operators, mitigating risks associated with high-speed rotations and heavy material handling. Additionally, ergonomic design elements, such as easy access to controls and adjustable working positions, reduce operator fatigue and maximize efficiency.5. Cost-Effective Solution:Investing in the Horizontal Boring Mill with Rotary Table translates into long-term cost savings for manufacturing companies. Its unparalleled precision minimizes material wastage and reduces the need for rework, saving valuable resources and improving profitability. Moreover, the machine's enhanced production capabilities accelerate project completion, helping businesses fulfill customer demands while maintaining a competitive edge.Conclusion:The introduction of the Horizontal Boring Mill with Rotary Table marks a significant milestone in the field of precision engineering and machining. With its advanced features, versatile applications, and commitment to safety, this groundbreaking machine promises to be a game-changer for manufacturing industries worldwide. By maximizing efficiency, precision, and productivity, it embraces the future of manufacturing, setting new benchmarks in the quest for excellence.
Exploring the Advantages of Horizontal Machining Centers in Industrial Settings
Title: Advancements in Horizontal Machining Centers Revolutionize Precision Manufacturing Introduction:With continuous advancements in technology, the manufacturing industry has witnessed a significant evolution in machining processes. Horizontal Machining Centers (HMCs), known for their high precision and efficiency, have played a crucial role in transforming contemporary manufacturing practices. This article explores the latest innovations in HMC technology and their contributions to precision manufacturing.1. Efficiency and Precision Redefined:HMCs have redefined the concept of efficiency and precision in modern manufacturing. Equipped with multiple cutting tools, these machines can simultaneously execute multiple operations, minimizing production time and increasing productivity. Their horizontal spindle orientation enables better chip evacuation, resulting in smoother and cleaner finishes. The technological advancements in HMCs have facilitated the production of complex components with impeccable accuracy, fulfilling the demands of today's industries.2. Integrated Automation and Robotics:To further enhance productivity and reduce manual labor, HMCs are now being integrated with advanced automation and robotic systems. The latest HMC models incorporate robotic loading and unloading systems, eliminating the need for human intervention and maximizing uptime. These automated solutions ensure continuous operation and reduce the risk of errors, ultimately enhancing the overall manufacturing process.3. Intelligent Control Systems:Intelligent control systems have revolutionized HMC operations, offering real-time monitoring and optimization of machining processes. The integration of Internet of Things (IoT) technology enables HMCs to connect with other machines, sensors, and data collection systems, facilitating data-driven decision-making. This connectivity allows manufacturers to gather valuable insights, thus optimizing production and minimizing downtime.4. Advanced Tooling Technology:The development of advanced tooling technology has greatly contributed to the efficiency and effectiveness of HMCs. Innovative cutting tools, such as multi-axis milling heads and high-speed machining spindles, enable HMCs to perform a wide range of operations with precision and versatility. Furthermore, the integration of tool pre-setters and tool life monitoring systems ensures efficient tool management, minimizing tool wear and reducing costs.5. Focus on Energy Efficiency:With sustainability gaining traction in the manufacturing industry, HMC manufacturers are increasingly focusing on energy-efficient solutions. The latest HMC models incorporate energy-saving features, such as regenerative braking systems and intelligent power management, reducing the overall energy consumption. These eco-friendly advancements not only contribute to a greener future but also offer cost savings for manufacturers.6. Enhanced Software Capabilities:The software capabilities of HMCs have evolved significantly, providing manufacturers with intuitive interfaces and advanced programming features. Programming languages such as CAD/CAM and G-code simplify the creation of complex machining operations. Additionally, simulation software allows manufacturers to validate programs and identify potential issues before execution, reducing errors and optimizing production.7. Industry-Specific Applications:HMCs find applications in various industries, including aerospace, automotive, and medical. The versatility of HMCs allows for the machining of large and heavy-duty parts, making them suitable for industries that require robust and precise components. Their ability to handle multiple operations simultaneously ensures faster turnaround times and reliable production processes, meeting the specific demands of each industry.Conclusion:Horizontal Machining Centers have undoubtedly transformed the precision manufacturing landscape. The combination of advanced technology and innovative features has revolutionized the efficiency, accuracy, and productivity of modern machining operations. With further advancements on the horizon, HMCs are poised to play a vital role in pushing the boundaries of precision manufacturing in the years to come.
Cutting-Edge Slant Bed CNC Machines Revolutionize Manufacturing Processes
Title: Advanced Slant Bed CNC Machines Offer Unmatched Precision and Efficiency in ManufacturingIntroduction:In the realm of advanced manufacturing, Slant Bed CNC Machines have emerged as game-changers, revolutionizing the way industries produce intricate components and parts. With their state-of-the-art technology and precision engineering, these machines offer unparalleled accuracy, efficiency, and versatility. This article discusses the features and benefits of Slant Bed CNC Machines, highlighting their impact in various sectors.Unveiling the Technology behind Slant Bed CNC Machines:Slant Bed CNC Machines, developed by leading industry experts, integrate cutting-edge technology to enhance manufacturing processes. These machines incorporate a computer numerical control (CNC) system that operates and controls tool movements with exceptional precision. The slanted design of the machine bed ensures ideal chip removal, reducing tool wear and enhancing overall machining stability.Features and Benefits that Enhance Manufacturing Efficiency:1. Design and Construction:Slant Bed CNC Machines are meticulously designed to ensure maximum rigidity, stability, and accuracy. The robust machine structure minimizes vibration during machining, guaranteeing superior surface finishing. Additionally, the slanted bed enhances accessibility, providing improved maneuverability and allowing easier chip removal.2. High-Speed Spindle:Equipped with high-speed spindle technology, Slant Bed CNC Machines enable rapid and precise material removal. This feature ensures reduced cycle times, increased productivity, and enhanced overall machining efficiency.3. Precision Linear Guides:Built with precision linear guides, Slant Bed CNC Machines guarantee smooth and precise movements across all axes. This enables intricate and complex geometries to be manufactured with exceptional accuracy, leading to high-quality end products.4. Multi-Axis Functionality:Slant Bed CNC Machines often incorporate multiple axes, including X, Y, and Z, as well as rotating tool heads. This multifunctionality allows for the production of a wider range of complex parts, reducing the need for additional machinery and streamlining manufacturing processes.5. User-Friendly Control System:Modern Slant Bed CNC Machines are equipped with user-friendly control systems, offering intuitive interfaces and programming options. This simplifies machine operation and programming, reducing potential errors and increasing overall productivity.Applications across Industries:1. Automotive Industry:Slant Bed CNC Machines play a crucial role in the automotive sector by manufacturing precision engine components, transmission parts, and intricate interiors. These machines ensure high accuracy and repeatability, meeting the stringent requirements of the automotive industry.2. Aerospace and Defense:The aerospace and defense sectors heavily rely on Slant Bed CNC Machines to craft intricate and complex parts, such as turbine blades, aerospace alloys, and structural components. The precision and efficiency of these machines contribute to the production of reliable and high-performance aerospace systems.3. Medical Equipment:Slant Bed CNC Machines are indispensable in the production of medical equipment, including surgical instruments, orthopedic implants, and prosthetic devices. The exceptional accuracy and surface quality provided by these machines yield artifacts essential for medical advancements.4. Electronics and Telecommunications:In the electronics and telecommunications industries, Slant Bed CNC Machines enable the manufacturing of microelectronic components, connectors, and precision hardware. The intricate nature of these components necessitates high accuracy and repeatability for seamless functionality.Conclusion:Slant Bed CNC Machines have proven to be a revolutionary force in the manufacturing industry, offering unmatched precision, efficiency, and versatility. By combining advanced technology, precise engineering, and user-friendly controls, these machines have become indispensable across a wide range of sectors. As manufacturers continue to demand precision and high-quality products, the role of Slant Bed CNC Machines in shaping the future of manufacturing remains vital.
Ultimate Guide to Manual Knee Mills: Everything You Need to Know
Title: Revolutionary Manual Knee Mills Introduced by Leading Manufacturing Company Introduction:Leading manufacturing company, XYZ Industries (name removed), is proud to announce the launch of their highly anticipated Manual Knee Mills, designed to revolutionize the milling industry. With their cutting-edge technology, advanced features, and unmatched precision, these mills are set to redefine machining capabilities. XYZ Industries aims to provide engineers and machinists with the tools they need to achieve their manufacturing goals efficiently and effectively. I. Features and Benefits:XYZ Industries' Manual Knee Mills offer a wide range of advanced features that cater to the evolving needs of the machining industry. Some key benefits of these mills include:1. Precision Engineering: The Manual Knee Mills incorporate state-of-the-art technology, allowing for exceptional precision and accuracy in the milling process. This precision is crucial for industries such as aerospace, automotive, and medical device manufacturing.2. Versatility: These mills are designed to handle a variety of materials, from soft metals to hardened steel, enabling engineers to perform a wide array of milling tasks with ease.3. User-Friendly Interface: XYZ Industries understands the importance of user experience. The Manual Knee Mills feature an intuitive interface that ensures operators can efficiently navigate through the machine's functions, reducing human error and enhancing productivity.4. Enhanced Visibility: The mills are equipped with LED lighting systems that provide optimal visibility, even in low-light conditions. This feature guarantees better control and precision during the milling process.5. Durability and Reliability: XYZ Industries ensures that their machines are manufactured using high-quality materials, making them robust and long-lasting. These mills are built to withstand the rigors of demanding machining operations.II. Cutting-Edge Technology:XYZ Industries has always been at the forefront of technological advancements in the manufacturing industry. The Manual Knee Mills reflect their commitment to innovation and utilizing the latest technologies. The following technologies are incorporated into these mills:1. Digital Readout (DRO) Systems: The mills are equipped with DRO systems, which provide real-time feedback on the machine's position, allowing operators to make precise adjustments quickly.2. Variable Speed Control: The mills offer variable speed control, allowing engineers to adapt the milling process according to the specific material being machined. This flexibility ensures optimal results and reduced machining time.3. Ergonomic Design: XYZ Industries prioritizes both functionality and user comfort. The Manual Knee Mills feature an ergonomic design with adjustable handles and controls, enabling operators to work in a comfortable and efficient manner.III. Industry Impact:XYZ Industries' Manual Knee Mills are expected to create a significant impact on the machining industry, for several reasons:1. Improved Productivity: The precision and user-friendly features of these mills increase productivity, reducing milling time and minimizing errors. This translates into faster production cycles and improved overall efficiency.2. Cost-Effectiveness: The mills offer an exceptional price-performance ratio, making them a cost-effective solution for machinists and manufacturers. The advanced features and versatility of these mills eliminate the need for additional equipment, providing significant cost savings.3. Advancement of Manufacturing Standards: The introduction of these mills raises the bar in terms of milling precision, consistency, and reliability. As a result, other manufacturers will be compelled to enhance their offerings to remain competitive in the market.In conclusion, XYZ Industries' release of their revolutionary Manual Knee Mills signifies a significant milestone in the manufacturing industry. These versatile tools with their advanced features and cutting-edge technology are set to transform machining capabilities. With unparalleled precision and user-friendly interfaces, engineers and machinists can look forward to increased productivity, improved cost-effectiveness, and the ability to achieve their manufacturing goals with utmost precision. XYZ Industries continues to spearhead innovation, pushing boundaries, and setting new standards in the machining industry.
Discover the Innovative Features of a 3-Axis CNC Vertical Milling Machine
Title: Revolutionary 3-Axis CNC Vertical Milling Machine Set to Streamline Manufacturing Processes Introduction:The manufacturing industry is on the brink of an innovative revolution as cutting-edge technologies continue to reshape the way products are made. In line with this transformative trend, an industry-leading company has unveiled a groundbreaking 3-axis CNC vertical milling machine that is set to revolutionize manufacturing processes. This state-of-the-art machinery, produced by a company committed to precision and efficiency, promises to deliver unparalleled productivity and accuracy to businesses across various sectors.Unleashing Cutting-Edge Capabilities:Known for its commitment to producing high-quality machinery, this company brings forth a 3-axis CNC vertical milling machine that boasts an impressive range of features. This machine seamlessly incorporates precision, reliability, and speed into one powerful unit, guaranteeing stunning results with every project.The machine features a robust base structure, expertly designed to provide enhanced stability during machining operations. This stability ensures accurate and consistent cutting, minimizing errors and eliminating the need for reworks. Additionally, the milling machine is equipped with an advanced control system that enables flawless 3-axis movement, allowing for the creation of intricate and complex designs.The machine's cutting-edge spindle ensures optimized material removal rates, resulting in faster production cycles and improved turnaround times. With the ability to rapidly change tools and seamlessly switch between various cutting techniques, this CNC milling machine empowers manufacturers to efficiently handle diverse production requirements.Intuitive Software Integration:In an era dominated by technological advancements, seamless software integration is essential for ensuring smooth operations. To this end, this 3-axis CNC milling machine comes equipped with state-of-the-art software that facilitates streamlined communication between the operator and the machine.The software, designed with a user-friendly interface, simplifies the programming process, eliminating the need for extensive training. The intuitive system allows manufacturers to effortlessly generate complex machining codes, significantly reducing the time needed for setup and programming. This user-centric approach empowers operators of all experience levels to achieve flawless results efficiently.Unmatched Precision and Versatility:The CNC vertical milling machine's exceptional precision sets it apart from traditional milling machines. The 3-axis movement system ensures exacting precision while simultaneously enabling the creation of intricate designs. Manufacturers can confidently rely on this machine to produce parts with tight tolerances, ensuring consistently high-quality end products.Furthermore, this CNC milling machine is highly versatile, capable of machining various materials, including metals, plastics, and composites. Its adaptability positions it as a go-to solution for a wide array of industries, such as aerospace, automotive, and electronics manufacturing. With this machine, manufacturers can readily explore new avenues and meet diverse customer demands.Enhanced Efficiency and Productivity:With the objective of increasing efficiency, this 3-axis CNC vertical milling machine boasts features that optimize productivity throughout the production process. Its advanced automation capabilities enable uninterrupted operations, reducing the need for manual intervention and minimizing downtime.The machine's automatic tool changer allows for quick and seamless tool transitions, eliminating time-consuming manual adjustments. Additionally, the CNC technology and advanced programming enable the machine to execute complex machining operations with minimal operator intervention. This streamlined workflow ensures manufacturers can complete projects promptly, enhancing overall productivity and profitability.Conclusion:The introduction of this revolutionary 3-axis CNC milling machine marks a new era in manufacturing, promising unmatched levels of precision, efficiency, and productivity. The integration of cutting-edge technology, combined with user-friendly software, allows for seamless operations and empowers manufacturers to create intricate designs effortlessly. With the impressive range of features and enhanced capabilities, this CNC vertical milling machine positions itself as the perfect solution to meet the diverse needs of modern manufacturing. As industries continue to evolve, this groundbreaking machinery paves the way for the future, offering a promising outlook for manufacturers looking to take their businesses to new heights.
Enhanced Precision and Versatility: Exploring the Capabilities of Vertical and Horizontal Jet Knee Milling Machine
[Company Name] Introduces Innovative Vertical and Horizontal Jet Knee Milling Machine[date], [Company Name], a leading manufacturer in the machining industry, announced the introduction of their latest product - the vertical and horizontal jet knee milling machine. This cutting-edge machine combines precision, efficiency, and versatility to meet the evolving needs of the modern manufacturing world.As technology progresses, so do the demands of manufacturers. The need for a milling machine that can perform both vertical and horizontal operations has become increasingly important. Recognizing this necessity, [Company Name] devoted extensive research and development to create a solution that seamlessly integrates the capabilities of both machine types into one comprehensive product.The newly introduced milling machine boasts a range of cutting-edge features designed to enhance productivity and ease of use. The dual functionality of vertical and horizontal operations allows for increased flexibility and reduces the need for separate machines, saving both time and costs for manufacturers. With this machine, [Company Name] aims to revolutionize the manufacturing process by streamlining operations and improving overall efficiency.Precision is paramount in the machining industry, and [Company Name] has taken great care to ensure that their milling machine delivers unparalleled accuracy. Equipped with state-of-the-art technology and robust construction, it guarantees precise and reliable results with every operation. The machine's high-resolution digital readout system offers precise positioning, allowing operators to achieve intricate designs with ease.In addition to its precision, the milling machine offers outstanding performance due to its powerful motor and advanced control systems. Thanks to its strong spindle, it can handle heavy-duty operations and accommodate a wide range of workpieces. The user-friendly control panel provides operators with intuitive access to various functions, making the machine suitable for both experienced professionals and newcomers to the industry.Safety is another critical aspect of any industrial machinery, and [Company Name] has gone above and beyond to ensure operator safety. The milling machine is equipped with advanced safety features, including an emergency stop button, protective guards, and interlocking systems, keeping operators out of harm's way during operation.To further enhance the user experience, [Company Name] invested in comprehensive customer support and training programs. The company's team of knowledgeable professionals is readily available to assist customers at every step of the way, from product selection to installation and maintenance. In addition, [Company Name] offers training sessions and educational resources to empower operators with the necessary skills to maximize the machine's potential.The introduction of the vertical and horizontal jet knee milling machine aligns with [Company Name]'s commitment to innovation and customer satisfaction. By continuously pushing boundaries and challenging industry norms, the company aims to equip manufacturers with cutting-edge tools that optimize their operations and contribute to their success.As the manufacturing industry evolves, [Company Name] remains dedicated to developing advanced solutions that address the ever-changing needs of its customers. The introduction of the vertical and horizontal jet knee milling machine signals a new era for [Company Name], where precision, efficiency, and versatility converge to shape the future of machining.With its robust features and exceptional performance, [Company Name]'s vertical and horizontal jet knee milling machine is set to revolutionize the manufacturing landscape and empower manufacturers worldwide.
Highly Efficient Profile Milling Machine for Precision Machining Processes
Profile Milling Machine Revolutionizing the Manufacturing IndustryIn a world driven by technological advancements, the manufacturing industry has always been at the forefront of innovation. Companies are constantly investing in cutting-edge machinery to improve productivity and precision in their production processes. One such groundbreaking invention is the Profile Milling Machine, an engineering marvel that is revolutionizing the manufacturing industry.The Profile Milling Machine, developed by a leading machinery manufacturer, is designed to precisely create complex and intricate profiles on various materials such as metal, plastic, and wood. It employs advanced technology and state-of-the-art features that make it highly efficient and reliable, ensuring consistent and accurate results.With a customizable software interface, the Profile Milling Machine allows operators to easily input and modify profiles according to their requirements. This feature not only saves time but also reduces the margin for error, making it ideal for mass production.One of the key advantages of the Profile Milling Machine is its high-speed machining capability. Equipped with powerful motors and high-speed spindles, it can swiftly and accurately cut through various materials, greatly improving efficiency and production rates. This allows manufacturers to meet tight deadlines without compromising on quality, giving them a competitive edge in the market.Furthermore, the Profile Milling Machine boasts exceptional precision and accuracy, thanks to its advanced servo control system. This technology enables the machine to maintain consistent cutting depths and speeds throughout the entire profiling process, resulting in a superior finish. Manufacturers can rely on the machine to meet the stringent requirements of industries such as aerospace, automotive, and electronics.The Profile Milling Machine also offers flexibility in terms of the types of profiles it can create. From simple curves to intricate patterns, the machine can accommodate a wide range of design specifications. This flexibility opens up endless possibilities for manufacturers, allowing them to realize their creative visions and produce unique and innovative products.Moreover, the Profile Milling Machine prioritizes user safety. It is equipped with various safety features such as emergency stop buttons, integrated safety guards, and enhanced operator controls. These measures ensure a secure working environment and minimize the risk of accidents or injuries.The company behind the Profile Milling Machine, with its extensive experience in precision engineering, has crafted a highly reliable and durable machine. Built to withstand heavy use and demanding production environments, the machine is designed for long-term use, reducing maintenance costs for manufacturers. Additionally, the company offers comprehensive after-sales support, including regular maintenance checks and swift replacement of spare parts when needed, ensuring uninterrupted production and minimal downtime.By investing in the Profile Milling Machine, manufacturers can experience a significant boost in productivity, quality, and efficiency. The machine's ability to create intricate profiles with speed and accuracy opens up new possibilities for product design and innovation. With improved production rates and consistently high-quality output, manufacturers can meet customer demands more effectively, enhancing their market competitiveness.In conclusion, the Profile Milling Machine is a game-changer in the manufacturing industry. Its advanced technology, high-speed machining, precision, versatility, and user safety features make it a valuable asset for any manufacturer seeking to revolutionize their production processes. Investing in this groundbreaking machine will undoubtedly pave the way for increased productivity, improved quality, and enhanced competitiveness in the fast-paced world of manufacturing.
Top Benchtop CNC Machines: Enhancing Precision and Efficiency
Title: Achieving Precision and Efficiency: Introducing the Innovative Benchtop CNC MachineIntroduction (80 words):In a constantly evolving technological landscape, the introduction of the Benchtop CNC Machine promises to revolutionize manufacturing processes across industries. Leveraging cutting-edge technology and unparalleled precision, this new addition to the market aims to transform prototyping, small-scale productions, and DIY projects. With its compact size and user-friendly interface, the Benchtop CNC Machine offers affordable, high-quality machining capabilities that were previously only accessible to larger manufacturing facilities. Read on to explore the features and benefits of this groundbreaking innovation.Paragraph 1 (100 words):Designed to meet the needs of hobbyists, machinists, and small business owners, the Benchtop CNC Machine combines powerful performance with ease of use. Developed by a team of industry experts with over two decades of experience, this innovative device utilizes advanced computer numerical control (CNC) technology, enabling users to create intricate designs with exceptional precision. With a compact footprint, the machine can be easily accommodated in limited workspace environments, making it a perfect choice for home-based workshops, startups, and educational institutions.Paragraph 2 (120 words):The Benchtop CNC Machine incorporates state-of-the-art features that set it apart from its competitors. Equipped with a high-speed spindle, it offers a wide range of speed adjustments to handle various materials and applications, including wood, plastics, aluminum, and even stainless steel. The machine's rigid structure ensures stability during operation, minimizing vibrations and resulting in superior surface finishes. Additionally, its user-friendly software interface simplifies the programming process, making it accessible to users of all skill levels. With support for industry-standard file formats, CAD/CAM integration, and an intuitive touchscreen display, the Benchtop CNC Machine streamlines workflow and facilitates the creation of intricate, precise parts.Paragraph 3 (140 words):The Benchtop CNC Machine boasts versatility, empowering users to explore their creativity and transform ideas into tangible objects. The system supports a wide range of design software, enabling users to import their customized 2D or 3D designs effortlessly. Whether it's crafting unique jewelry, prototyping new products, or producing custom components, this machine delivers exceptional speed and accuracy. Moreover, its integrated safety features, such as emergency stop buttons and protective enclosures, ensure secure operation for both experienced and novice users. Thanks to its efficient design and intuitive interface, the Benchtop CNC Machine drastically reduces material waste, thus contributing to a more sustainable manufacturing process.Paragraph 4 (160 words):The development of this cutting-edge technology was driven by the company's commitment to bringing professional-grade performance to small-scale manufacturers. Recognizing the increasing demand for precision machining solutions, the Benchtop CNC Machine offers an affordable alternative without compromising on quality. By partnering with a team of engineers and designers, the company ensured that the machine met the specific needs and requirements of users across various industries.Conclusion (100 words):The introduction of the Benchtop CNC Machine marks a significant leap towards empowering small-scale manufacturers and DIY enthusiasts with professional-grade machining capabilities. Its compact size, versatility, and ease of use make it ideal for a wide range of applications, from prototyping to educational purposes. With its advanced features, such as high-speed spindle, user-friendly software, and a rigid structure, this device ensures precision and efficiency in every project. As industries continue to evolve, the Benchtop CNC Machine enables businesses to remain competitive by delivering high-quality results at an affordable price point.
Enhancing Precision and Efficiency: A Comprehensive Guide to Vertical Machining Centers
Title: Cutting-Edge Vertical Machining Center Redefines High Precision ManufacturingIntroduction:In this modern era of advanced technology, the manufacturing industry continues to drive significant growth and innovation. Emphasizing accuracy, efficiency, and versatility, cutting-edge vertical machining centers have become indispensable tools for many renowned manufacturers. This article delves into the remarkable features of a prominent industry player's latest offering, exploring how it revolutionizes high-precision manufacturing processes.1. Superior Design and Unparalleled Precision:The newly developed Vertical Machining Center (VMC) is a testament to the company's unwavering commitment to excellence. Built with a robust steel frame and incorporating rigid cast iron components, the machine guarantees high stability and vibration resistance. This not only extends the machine's lifespan but also ensures unparalleled precision in every manufactured component.2. Unmatched Speed and Efficiency:Equipped with a powerful and rapid spindle, the VMC delivers unrivaled speed and efficiency in machining operations. Its advanced control software enables seamless integration of CAD/CAM programs, significantly reducing setup time and maximizing productivity. With high-speed chip removal capabilities, the VMC guarantees reduced machining time, translating into higher throughput and reduced manufacturing costs.3. Advanced Control and Programming:The VMC's user-friendly control interface, combined with advanced programming capabilities, simplifies complex manufacturing tasks. The intuitive touch screen allows operators to effortlessly schedule operations, monitor progress, and make real-time adjustments. With its efficient tool management system and adaptive control, the VMC ensures accurate machining and optimizes tool utilization, minimizing tool changes and downtime.4. Versatile Tooling Options:The VMC offers versatile tooling options, making it suitable for diverse manufacturing needs. With an automatic tool changer, the machine swiftly swaps tools to accommodate varying machining requirements without interrupting the production process. The compatibility with a wide range of tool diameters and lengths ensures flexibility and adaptability, enabling manufacturers to tackle complex designs and produce intricate components.5. Enhanced Safety Features:Safety is of paramount importance in any manufacturing environment. To address this concern, the VMC incorporates a comprehensive range of safety features. The machine employs advanced sensors and interlocks to prevent accidental collisions and tool breakages. Additionally, the VMC's emergency stop mechanisms and safety guards provide an enhanced level of protection for operators, ensuring a secure working environment.6. Commitment to Sustainability:As manufacturers strive for sustainable practices, the VMC incorporates various energy-saving features that reduce its environmental impact. The machine incorporates smart technologies that optimize power consumption during idle times, minimizing energy wastage. Furthermore, the VMC's efficient coolant recycling system not only reduces coolant consumption but also minimizes the release of hazardous waste, promoting sustainability throughout the manufacturing process.7. Capitalizing on Digital Transformation:The VMC embraces the cutting-edge capabilities of Industry 4.0, contributing to seamless digital transformations in manufacturing facilities. Its compatibility with IoT devices and data analytics systems allows operators to monitor and optimize machine performance remotely. Real-time data collection facilitates predictive maintenance, minimizing machine downtime and enhancing overall operational efficiency.Conclusion:The unveiling of the state-of-the-art vertical machining center represents a significant milestone in the evolution of high-precision manufacturing. With its unmatched precision, speed, versatility, and unrivaled performance, the VMC is poised to revolutionize the manufacturing industry. By delivering exceptional quality, high efficiency, and sustainability, this cutting-edge machine cements the company's reputation as a leader in the field of advanced manufacturing technology.
Discover the Latest Advancements in Machining Centers: Your Ultimate Guide
Title: Revolutionary Machining Center Unveiled: A Game-Changer in Industrial PrecisionIntroduction:In a groundbreaking move, a leading engineering solutions provider has unveiled its latest innovation, a state-of-the-art machining center that is set to redefine precision and efficiency in the industrial sector. With a commitment to technological advancement and customer satisfaction, the company has developed this cutting-edge solution to meet the evolving needs of the manufacturing industry. This article explores the features and potential impact of this remarkable machining center on various sectors of the economy.Unleashing Unparalleled Precision:The new machining center stands out for its exceptional precision, enabling manufacturers to produce intricate parts and components with unparalleled accuracy. Equipped with advanced computer numerical control (CNC) technology, the machining center offers high-speed machining capabilities that significantly reduce production time while guaranteeing precision within microns. This feature is poised to transform industries such as aerospace, automotive, and medical, where intricate details and precise measurements are critical.State-of-the-Art Automation:Automation has become an integral part of industrial processes, and the new machining center takes it to a whole new level. The incorporation of robotic arms and machine vision systems streamlines operations by automating material handling, tool changes, and quality control. This automation not only expedites production but also minimizes the risk of human error, ensuring consistent quality and reducing costs associated with manual labor.Enhanced Efficiency and Productivity:With optimized tooling and innovative cutting strategies, the new machining center significantly boosts efficiency and productivity in manufacturing processes. Its multi-axis capabilities and simultaneous machining options allow for simultaneous operations, reducing setup time and increasing throughput. This enhanced productivity directly translates to cost savings and enables manufacturers to meet growing demands efficiently.Seamless Integration with Industry 4.0:In an era of digitalization, the new machining center is designed to seamlessly integrate with the principles of Industry 4.0. With built-in sensors and connectivity features, it enables real-time monitoring, predictive maintenance, and data-driven decision-making. This integration empowers manufacturers to embrace the concept of smart factories and optimize their operations for maximum efficiency, leading to reduced downtime and improved overall performance.Commitment to Sustainability:The company's commitment to responsible manufacturing and environmental sustainability is apparent in the design and functionalities of the machining center. By incorporating energy-efficient components and minimizing material waste through advanced cutting strategies, this solution champions sustainability without compromising on performance. It aligns with global efforts to reduce the carbon footprint of industries and underscores the company's dedication to a greener future.Empowering Skilled Workforce:While automation reduces dependency on manual labor, the new machining center seeks to empower the skilled workforce by offering comprehensive training and support programs. The company recognizes the importance of human expertise in leveraging the full potential of this advanced technology. By providing training on programming, maintenance, and troubleshooting, they are ensuring that individuals adapt seamlessly to the evolving industry landscape.Expanding Market Opportunities:The unrivaled precision and versatility of the new machining center open doors to countless market opportunities. Its ability to produce intricate, complex, and high-performance parts makes it ideal for industries such as aerospace, automotive, electronics, and medical devices. It allows manufacturers to explore new avenues, enhance product offerings, and gain a competitive edge in an increasingly demanding market.Conclusion:The unveiling of this revolutionary machining center marks a significant step forward in the evolution of industrial precision and productivity. With its exceptional precision, state-of-the-art automation, seamless integration with Industry 4.0, commitment to sustainability, and focus on empowering the skilled workforce, this innovation is set to revolutionize manufacturing processes across various sectors. As the industry embraces this game-changing technology, it is poised to witness increased efficiency, reduced costs, and enhanced product quality, paving the way for a brighter and more prosperous future.
Exploring the Advantages of a Rotary Table Horizontal Boring Mill
Title: Innovative Horizontal Boring Mill with Rotary Table Enhances Precision and EfficiencyIntroduction:In today's ever-evolving landscape of manufacturing and industrial solutions, companies are continuously seeking innovative machinery that maximizes precision, efficiency, and productivity. Addressing these demands, an industry-leading company has introduced its highly advanced Horizontal Boring Mill with Rotary Table—an engineering marvel that redefines machining capabilities and sets new standards for the manufacturing sector.Context:The Horizontal Boring Mill with Rotary Table, developed by an industry pioneer, represents a significant breakthrough in machining technology. With its cutting-edge features and wide-ranging applications, this state-of-the-art equipment promises to revolutionize various sectors, including aerospace, automotive, energy, and beyond.Main Body:1. Precision Engineering at its Finest: The Horizontal Boring Mill with Rotary Table stands out for its exceptional precision and accuracy. Equipped with advanced CNC controls and integrated measurement systems, this revolutionary machine ensures that every component passes the most stringent quality standards. Its meticulous drilling, milling, and boring capabilities guarantee optimal fit and tolerance, resulting in superior end products.2. Advanced Features Enhancing Efficiency:The incorporation of innovative features in the Horizontal Boring Mill with Rotary Table translates into enhanced productivity and efficiency for industrial operations. Equipped with a robust rotary table, a wide range of multi-axis machining operations can be accomplished in a single setup, reducing production time and maximizing output. The machine's high-speed spindle motor enables rapid cutting while maintaining accuracy, further improving efficiency.3. Versatile Applications:With its adaptability and versatility, the Horizontal Boring Mill with Rotary Table caters to a variety of manufacturing needs. From producing complex components for the aerospace industry to manufacturing large-scale automotive parts, this machine is designed to handle a diverse range of projects effectively. Furthermore, its ability to accommodate different materials, including steel, aluminum, and composites, grants companies unmatched flexibility.4. Safety and Ergonomics:While pushing the boundaries of machining capabilities, the Horizontal Boring Mill with Rotary Table also prioritizes operator safety. Incorporating state-of-the-art safety systems ensures a secure working environment for the machine's operators, mitigating risks associated with high-speed rotations and heavy material handling. Additionally, ergonomic design elements, such as easy access to controls and adjustable working positions, reduce operator fatigue and maximize efficiency.5. Cost-Effective Solution:Investing in the Horizontal Boring Mill with Rotary Table translates into long-term cost savings for manufacturing companies. Its unparalleled precision minimizes material wastage and reduces the need for rework, saving valuable resources and improving profitability. Moreover, the machine's enhanced production capabilities accelerate project completion, helping businesses fulfill customer demands while maintaining a competitive edge.Conclusion:The introduction of the Horizontal Boring Mill with Rotary Table marks a significant milestone in the field of precision engineering and machining. With its advanced features, versatile applications, and commitment to safety, this groundbreaking machine promises to be a game-changer for manufacturing industries worldwide. By maximizing efficiency, precision, and productivity, it embraces the future of manufacturing, setting new benchmarks in the quest for excellence.
Exploring the Advantages of Horizontal Machining Centers in Industrial Settings
Title: Advancements in Horizontal Machining Centers Revolutionize Precision Manufacturing Introduction:With continuous advancements in technology, the manufacturing industry has witnessed a significant evolution in machining processes. Horizontal Machining Centers (HMCs), known for their high precision and efficiency, have played a crucial role in transforming contemporary manufacturing practices. This article explores the latest innovations in HMC technology and their contributions to precision manufacturing.1. Efficiency and Precision Redefined:HMCs have redefined the concept of efficiency and precision in modern manufacturing. Equipped with multiple cutting tools, these machines can simultaneously execute multiple operations, minimizing production time and increasing productivity. Their horizontal spindle orientation enables better chip evacuation, resulting in smoother and cleaner finishes. The technological advancements in HMCs have facilitated the production of complex components with impeccable accuracy, fulfilling the demands of today's industries.2. Integrated Automation and Robotics:To further enhance productivity and reduce manual labor, HMCs are now being integrated with advanced automation and robotic systems. The latest HMC models incorporate robotic loading and unloading systems, eliminating the need for human intervention and maximizing uptime. These automated solutions ensure continuous operation and reduce the risk of errors, ultimately enhancing the overall manufacturing process.3. Intelligent Control Systems:Intelligent control systems have revolutionized HMC operations, offering real-time monitoring and optimization of machining processes. The integration of Internet of Things (IoT) technology enables HMCs to connect with other machines, sensors, and data collection systems, facilitating data-driven decision-making. This connectivity allows manufacturers to gather valuable insights, thus optimizing production and minimizing downtime.4. Advanced Tooling Technology:The development of advanced tooling technology has greatly contributed to the efficiency and effectiveness of HMCs. Innovative cutting tools, such as multi-axis milling heads and high-speed machining spindles, enable HMCs to perform a wide range of operations with precision and versatility. Furthermore, the integration of tool pre-setters and tool life monitoring systems ensures efficient tool management, minimizing tool wear and reducing costs.5. Focus on Energy Efficiency:With sustainability gaining traction in the manufacturing industry, HMC manufacturers are increasingly focusing on energy-efficient solutions. The latest HMC models incorporate energy-saving features, such as regenerative braking systems and intelligent power management, reducing the overall energy consumption. These eco-friendly advancements not only contribute to a greener future but also offer cost savings for manufacturers.6. Enhanced Software Capabilities:The software capabilities of HMCs have evolved significantly, providing manufacturers with intuitive interfaces and advanced programming features. Programming languages such as CAD/CAM and G-code simplify the creation of complex machining operations. Additionally, simulation software allows manufacturers to validate programs and identify potential issues before execution, reducing errors and optimizing production.7. Industry-Specific Applications:HMCs find applications in various industries, including aerospace, automotive, and medical. The versatility of HMCs allows for the machining of large and heavy-duty parts, making them suitable for industries that require robust and precise components. Their ability to handle multiple operations simultaneously ensures faster turnaround times and reliable production processes, meeting the specific demands of each industry.Conclusion:Horizontal Machining Centers have undoubtedly transformed the precision manufacturing landscape. The combination of advanced technology and innovative features has revolutionized the efficiency, accuracy, and productivity of modern machining operations. With further advancements on the horizon, HMCs are poised to play a vital role in pushing the boundaries of precision manufacturing in the years to come.
Cutting-Edge Slant Bed CNC Machines Revolutionize Manufacturing Processes
Title: Advanced Slant Bed CNC Machines Offer Unmatched Precision and Efficiency in ManufacturingIntroduction:In the realm of advanced manufacturing, Slant Bed CNC Machines have emerged as game-changers, revolutionizing the way industries produce intricate components and parts. With their state-of-the-art technology and precision engineering, these machines offer unparalleled accuracy, efficiency, and versatility. This article discusses the features and benefits of Slant Bed CNC Machines, highlighting their impact in various sectors.Unveiling the Technology behind Slant Bed CNC Machines:Slant Bed CNC Machines, developed by leading industry experts, integrate cutting-edge technology to enhance manufacturing processes. These machines incorporate a computer numerical control (CNC) system that operates and controls tool movements with exceptional precision. The slanted design of the machine bed ensures ideal chip removal, reducing tool wear and enhancing overall machining stability.Features and Benefits that Enhance Manufacturing Efficiency:1. Design and Construction:Slant Bed CNC Machines are meticulously designed to ensure maximum rigidity, stability, and accuracy. The robust machine structure minimizes vibration during machining, guaranteeing superior surface finishing. Additionally, the slanted bed enhances accessibility, providing improved maneuverability and allowing easier chip removal.2. High-Speed Spindle:Equipped with high-speed spindle technology, Slant Bed CNC Machines enable rapid and precise material removal. This feature ensures reduced cycle times, increased productivity, and enhanced overall machining efficiency.3. Precision Linear Guides:Built with precision linear guides, Slant Bed CNC Machines guarantee smooth and precise movements across all axes. This enables intricate and complex geometries to be manufactured with exceptional accuracy, leading to high-quality end products.4. Multi-Axis Functionality:Slant Bed CNC Machines often incorporate multiple axes, including X, Y, and Z, as well as rotating tool heads. This multifunctionality allows for the production of a wider range of complex parts, reducing the need for additional machinery and streamlining manufacturing processes.5. User-Friendly Control System:Modern Slant Bed CNC Machines are equipped with user-friendly control systems, offering intuitive interfaces and programming options. This simplifies machine operation and programming, reducing potential errors and increasing overall productivity.Applications across Industries:1. Automotive Industry:Slant Bed CNC Machines play a crucial role in the automotive sector by manufacturing precision engine components, transmission parts, and intricate interiors. These machines ensure high accuracy and repeatability, meeting the stringent requirements of the automotive industry.2. Aerospace and Defense:The aerospace and defense sectors heavily rely on Slant Bed CNC Machines to craft intricate and complex parts, such as turbine blades, aerospace alloys, and structural components. The precision and efficiency of these machines contribute to the production of reliable and high-performance aerospace systems.3. Medical Equipment:Slant Bed CNC Machines are indispensable in the production of medical equipment, including surgical instruments, orthopedic implants, and prosthetic devices. The exceptional accuracy and surface quality provided by these machines yield artifacts essential for medical advancements.4. Electronics and Telecommunications:In the electronics and telecommunications industries, Slant Bed CNC Machines enable the manufacturing of microelectronic components, connectors, and precision hardware. The intricate nature of these components necessitates high accuracy and repeatability for seamless functionality.Conclusion:Slant Bed CNC Machines have proven to be a revolutionary force in the manufacturing industry, offering unmatched precision, efficiency, and versatility. By combining advanced technology, precise engineering, and user-friendly controls, these machines have become indispensable across a wide range of sectors. As manufacturers continue to demand precision and high-quality products, the role of Slant Bed CNC Machines in shaping the future of manufacturing remains vital.