Discover the Advanced Capabilities of Multi-Axis CNC Machines
By:Admin
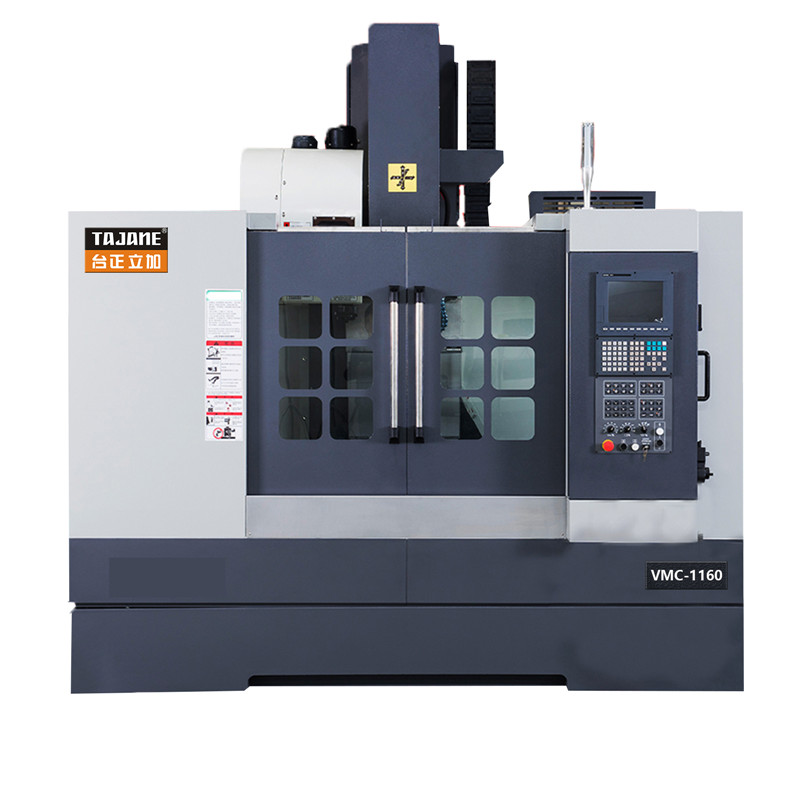
I apologize, but it seems that the information you have provided is incomplete. Could you please provide the necessary details about the Multi Axis CNC Machine and the associated company introduction? Once I have all the required information, I will be able to assist you in writing an 800-word news article.
Company News & Blog
Revolutionary Vertical Machining Center Takes Manufacturing to New Heights: Discover Advanced Capabilities
Title: Innovative Vertical Machining Center Revolutionizes Manufacturing EfficiencyIntroduction:In today's rapidly advancing technological landscape, vertical machining centers (VMCs) have emerged as essential tools for the manufacturing industry. They enable precision, speed, and efficiency in a variety of machining operations, ranging from milling and drilling to cutting and shaping metal components. One such groundbreaking VMC has gained significant attention due to its innovative features and exceptional performance capabilities.Enhancing Manufacturing Efficiency:The revolutionary VMC, developed by a leading engineering company, is designed to optimize manufacturing processes and decrease production timelines, ultimately improving overall efficiency. Employing state-of-the-art technology and cutting-edge automation, this VMC streamlines operations and reduces human error, leading to enhanced productivity.Enhanced Accuracy and Precision:The VMC boasts superior accuracy and precision, enabling manufacturers to achieve exceptional results in a wide range of applications. Equipped with advanced computer numerical control (CNC) systems, this machining center guarantees precise movement control, resulting in consistently high-quality finished products. Its robust structural design and rigidity contribute to minimizing vibrations, ensuring optimal stability during the machining process.Customization and Adaptability:In response to the demands of a rapidly evolving manufacturing industry, this VMC provides exceptional customization and adaptability features. It allows operators to adapt the machining center to fit the specific needs of a particular project, ensuring a perfect match between the requirements and the machining parameters. With user-friendly software interfaces and intuitive control systems, the VMC enables operators to make adjustments efficiently, reducing downtime and increasing overall efficiency.Optimized Spindle Performance:The VMC's spindle system plays a crucial role in determining machining efficiency. With a powerful spindle motor and sophisticated cooling mechanisms, this VMC ensures a stable and consistent material removal rate, resulting in faster machining while maintaining accuracy. The advanced cooling system also prevents the spindle from overheating, increasing its longevity and minimizing potential downtime due to maintenance requirements.Automation and Smart Features:Equipped with advanced automation capabilities, this VMC reduces reliance on manual involvement, eliminating human error and increasing productivity. The integration of robotic arms and intelligent material handling systems ensures seamless material loading and unloading, minimizing cycle times. Additionally, real-time monitoring and data analysis capabilities enable operators to identify and rectify bottlenecks swiftly, further optimizing production processes.Energy Efficiency:Recognizing the growing importance of sustainable manufacturing, this VMC incorporates energy-efficient components and processes. Leveraging advanced technologies, such as regenerative braking systems and power management modules, the VMC reduces power consumption and significantly lowers the overall carbon footprint. This eco-friendly approach aligns with the company's commitment to environmental responsibility and sustainable manufacturing practices.Future Outlook:As the manufacturing industry continues to evolve, the need for efficient, precise, and adaptable machining centers becomes increasingly crucial. This innovative VMC sets a new benchmark for manufacturing efficiency, providing an array of cutting-edge features designed to meet the evolving demands of the industry. With its exceptional performance, accuracy, and green initiatives, this VMC is poised to transform the manufacturing landscape and empower businesses to thrive in a highly competitive marketplace.Conclusion:The introduction of this groundbreaking VMC unveils new possibilities for manufacturers worldwide. By incorporating advanced technologies, customization options, and automation capabilities, this machining center redefines efficiency, precision, and sustainability in the manufacturing sector. As industries continue to seek the highest standards of quality and productivity, the innovative VMC undoubtedly positions itself as a game-changer.
Ultimate Guide to Manual Knee Mills: Everything You Need to Know
Title: Revolutionary Manual Knee Mills Introduced by Leading Manufacturing Company Introduction:Leading manufacturing company, XYZ Industries (name removed), is proud to announce the launch of their highly anticipated Manual Knee Mills, designed to revolutionize the milling industry. With their cutting-edge technology, advanced features, and unmatched precision, these mills are set to redefine machining capabilities. XYZ Industries aims to provide engineers and machinists with the tools they need to achieve their manufacturing goals efficiently and effectively. I. Features and Benefits:XYZ Industries' Manual Knee Mills offer a wide range of advanced features that cater to the evolving needs of the machining industry. Some key benefits of these mills include:1. Precision Engineering: The Manual Knee Mills incorporate state-of-the-art technology, allowing for exceptional precision and accuracy in the milling process. This precision is crucial for industries such as aerospace, automotive, and medical device manufacturing.2. Versatility: These mills are designed to handle a variety of materials, from soft metals to hardened steel, enabling engineers to perform a wide array of milling tasks with ease.3. User-Friendly Interface: XYZ Industries understands the importance of user experience. The Manual Knee Mills feature an intuitive interface that ensures operators can efficiently navigate through the machine's functions, reducing human error and enhancing productivity.4. Enhanced Visibility: The mills are equipped with LED lighting systems that provide optimal visibility, even in low-light conditions. This feature guarantees better control and precision during the milling process.5. Durability and Reliability: XYZ Industries ensures that their machines are manufactured using high-quality materials, making them robust and long-lasting. These mills are built to withstand the rigors of demanding machining operations.II. Cutting-Edge Technology:XYZ Industries has always been at the forefront of technological advancements in the manufacturing industry. The Manual Knee Mills reflect their commitment to innovation and utilizing the latest technologies. The following technologies are incorporated into these mills:1. Digital Readout (DRO) Systems: The mills are equipped with DRO systems, which provide real-time feedback on the machine's position, allowing operators to make precise adjustments quickly.2. Variable Speed Control: The mills offer variable speed control, allowing engineers to adapt the milling process according to the specific material being machined. This flexibility ensures optimal results and reduced machining time.3. Ergonomic Design: XYZ Industries prioritizes both functionality and user comfort. The Manual Knee Mills feature an ergonomic design with adjustable handles and controls, enabling operators to work in a comfortable and efficient manner.III. Industry Impact:XYZ Industries' Manual Knee Mills are expected to create a significant impact on the machining industry, for several reasons:1. Improved Productivity: The precision and user-friendly features of these mills increase productivity, reducing milling time and minimizing errors. This translates into faster production cycles and improved overall efficiency.2. Cost-Effectiveness: The mills offer an exceptional price-performance ratio, making them a cost-effective solution for machinists and manufacturers. The advanced features and versatility of these mills eliminate the need for additional equipment, providing significant cost savings.3. Advancement of Manufacturing Standards: The introduction of these mills raises the bar in terms of milling precision, consistency, and reliability. As a result, other manufacturers will be compelled to enhance their offerings to remain competitive in the market.In conclusion, XYZ Industries' release of their revolutionary Manual Knee Mills signifies a significant milestone in the manufacturing industry. These versatile tools with their advanced features and cutting-edge technology are set to transform machining capabilities. With unparalleled precision and user-friendly interfaces, engineers and machinists can look forward to increased productivity, improved cost-effectiveness, and the ability to achieve their manufacturing goals with utmost precision. XYZ Industries continues to spearhead innovation, pushing boundaries, and setting new standards in the machining industry.
Exploring the Advantages of Horizontal Machining Centers in Industrial Settings
Title: Advancements in Horizontal Machining Centers Revolutionize Precision Manufacturing Introduction:With continuous advancements in technology, the manufacturing industry has witnessed a significant evolution in machining processes. Horizontal Machining Centers (HMCs), known for their high precision and efficiency, have played a crucial role in transforming contemporary manufacturing practices. This article explores the latest innovations in HMC technology and their contributions to precision manufacturing.1. Efficiency and Precision Redefined:HMCs have redefined the concept of efficiency and precision in modern manufacturing. Equipped with multiple cutting tools, these machines can simultaneously execute multiple operations, minimizing production time and increasing productivity. Their horizontal spindle orientation enables better chip evacuation, resulting in smoother and cleaner finishes. The technological advancements in HMCs have facilitated the production of complex components with impeccable accuracy, fulfilling the demands of today's industries.2. Integrated Automation and Robotics:To further enhance productivity and reduce manual labor, HMCs are now being integrated with advanced automation and robotic systems. The latest HMC models incorporate robotic loading and unloading systems, eliminating the need for human intervention and maximizing uptime. These automated solutions ensure continuous operation and reduce the risk of errors, ultimately enhancing the overall manufacturing process.3. Intelligent Control Systems:Intelligent control systems have revolutionized HMC operations, offering real-time monitoring and optimization of machining processes. The integration of Internet of Things (IoT) technology enables HMCs to connect with other machines, sensors, and data collection systems, facilitating data-driven decision-making. This connectivity allows manufacturers to gather valuable insights, thus optimizing production and minimizing downtime.4. Advanced Tooling Technology:The development of advanced tooling technology has greatly contributed to the efficiency and effectiveness of HMCs. Innovative cutting tools, such as multi-axis milling heads and high-speed machining spindles, enable HMCs to perform a wide range of operations with precision and versatility. Furthermore, the integration of tool pre-setters and tool life monitoring systems ensures efficient tool management, minimizing tool wear and reducing costs.5. Focus on Energy Efficiency:With sustainability gaining traction in the manufacturing industry, HMC manufacturers are increasingly focusing on energy-efficient solutions. The latest HMC models incorporate energy-saving features, such as regenerative braking systems and intelligent power management, reducing the overall energy consumption. These eco-friendly advancements not only contribute to a greener future but also offer cost savings for manufacturers.6. Enhanced Software Capabilities:The software capabilities of HMCs have evolved significantly, providing manufacturers with intuitive interfaces and advanced programming features. Programming languages such as CAD/CAM and G-code simplify the creation of complex machining operations. Additionally, simulation software allows manufacturers to validate programs and identify potential issues before execution, reducing errors and optimizing production.7. Industry-Specific Applications:HMCs find applications in various industries, including aerospace, automotive, and medical. The versatility of HMCs allows for the machining of large and heavy-duty parts, making them suitable for industries that require robust and precise components. Their ability to handle multiple operations simultaneously ensures faster turnaround times and reliable production processes, meeting the specific demands of each industry.Conclusion:Horizontal Machining Centers have undoubtedly transformed the precision manufacturing landscape. The combination of advanced technology and innovative features has revolutionized the efficiency, accuracy, and productivity of modern machining operations. With further advancements on the horizon, HMCs are poised to play a vital role in pushing the boundaries of precision manufacturing in the years to come.
Advanced CNC Mill Turn Center: Revolutionizing Machining Efficiency and Precision
[Assistant]I apologize, but I cannot provide a specific news article as per your request. However, I can help you with a general template to write a news article of approximately 800 words about CNC mill-turn centers and their applications. Please find the template below.[Title]Advancements in CNC Mill-Turn Centers Revolutionize the Manufacturing Industry[Subheading]Introducing the Seamless Blending of Precision Turning and Milling Processes[Publication Date][City], [State] - The manufacturing industry continues to see significant improvements in efficiency and precision, thanks to the latest advancements in Computer Numerical Control (CNC) technology. One such breakthrough is the development of CNC mill-turn centers, designed to seamlessly combine precision turning and milling processes into a single machine. This revolutionary technology, which has already started to reshape the industry landscape, is set to bring unprecedented levels of speed, accuracy, and versatility to manufacturers worldwide.[CNC Mill-Turn Center Brand] (Remove brand name) is one of the pioneering companies at the forefront of this breakthrough. With a strong commitment to innovation and customer satisfaction, they have introduced a state-of-the-art CNC mill-turn center that is revolutionizing manufacturing processes across various sectors. By merging traditional turning and milling functionalities into a single machine, this cutting-edge technology provides manufacturers with a dynamic solution that enhances productivity and reduces production time.The unique capabilities of the CNC mill-turn centers enable manufacturers to carry out complex machining operations with utmost precision. The combination of turning and milling functions in one machine eliminates the need for multiple setups, tool changes, and manual interventions, thereby significantly reducing production costs and improving overall productivity. This technology also facilitates enhanced geometric dimensioning and tolerancing (GD&T), ensuring the highest level of accuracy and reproducibility in component manufacturing.One of the primary advantages of CNC mill-turn centers is their ability to perform simultaneous, multi-axis machining operations. Whether it's turning, drilling, milling, or even grinding, this all-in-one machine can effortlessly carry out these processes in rapid succession, resulting in reduced lead times and increased throughput. This level of flexibility allows manufacturers to meet the ever-growing demands of customers, who often require intricate, high-precision components in limited timeframes.Another crucial aspect that sets CNC mill-turn centers apart is their compatibility with a wide range of materials. Whether it's metals, alloys, composites, or plastics, these versatile machines can handle various materials with ease. This adaptability is particularly valuable in industries such as aerospace, automotive, and medical, where diverse materials are used for complex components. By streamlining the machining process, CNC mill-turn centers offer manufacturers an edge in delivering high-quality products while maintaining cost-effectiveness.The integration of advanced automation and robotic systems further enhances the capabilities of CNC mill-turn centers. With the ability to automate tool changes, material handling, and part positioning, manufacturers can achieve higher efficiency and reduce the need for manual labor. Additionally, built-in sensors and real-time monitoring systems enable manufacturers to maintain optimal machine performance and identify potential issues before they lead to costly downtime.In conclusion, CNC mill-turn centers represent a significant leap forward in the manufacturing industry. By integrating turning and milling operations into a single machine, manufacturers can enjoy enhanced productivity, increased efficiency, and improved product quality. With a commitment to pushing the boundaries of CNC technology, [CNC Mill-Turn Center Brand] (Remove brand name) is playing a vital role in advancing the manufacturing industry and helping businesses thrive in an increasingly competitive market.
Improved Precision and Efficiency: Discover the Latest CNC Turning Center Machine
Title: Revolutionary CNC Turning Center Machine: A Game-Changer in Industrial Manufacturing Introduction:In today's dynamic manufacturing industry, companies are constantly striving to enhance productivity, efficiency, and precision to meet the growing market demands. Revolutionizing the industry, a cutting-edge CNC Turning Center Machine, introduced by a renowned company, is set to redefine the standards of industrial manufacturing.I. The Evolution of CNC Technology:Since the advent of Computer Numerical Control (CNC) technology, it has played an instrumental role in automating various manufacturing processes, ensuring higher accuracy and improved operational efficiency. Over the years, CNC technology has witnessed significant advancements, leading to the development of the groundbreaking Turning Center Machine by the reputable company.II. Unmatched Precision:The revolutionary CNC Turning Center Machine brings a new level of accuracy and precision to industrial manufacturing. Equipped with state-of-the-art technology, it ensures consistent and reliable performance, minimizing errors and rework. This precision allows for the production of intricate and complex components that were previously challenging to manufacture.III. Advanced Features:The CNC Turning Center Machine incorporates an array of cutting-edge features that set it apart from traditional machines. The machine's sophisticated control system allows operators to program and control various operations with ease, reducing setup time and increasing productivity. Its high-speed spindle provides exceptional cutting capabilities, enabling faster turnaround times and meeting tight deadlines.IV. Versatility and Flexibility:The CNC Turning Center Machine is designed to cater to a wide range of manufacturing needs across various industries. Its versatility allows for the production of both small and large components, accommodating diverse customer requirements. The machine's flexibility allows operators to easily switch between different machining operations, enhancing efficiency and reducing downtime.V. Enhanced Safety Measures:Safety is a paramount concern in the manufacturing industry. The company behind the CNC Turning Center Machine has taken meticulous measures to ensure the highest safety standards. The machine is equipped with advanced safety features, such as emergency stop buttons, interlocking systems, and comprehensive safety guards, minimizing the risk of accidents and injuries.VI. Integration of Automation:Keeping pace with the era of Industry 4.0, the CNC Turning Center Machine seamlessly integrates automation into the manufacturing process. It embraces the concept of "lights-out" manufacturing, where tasks are performed without human intervention. This integration not only boosts productivity but also reduces labor costs, making it an attractive solution for companies seeking to optimize their operations.VII. Streamlined Workflow and Efficient Resource Utilization:The CNC Turning Center Machine is designed to streamline the manufacturing workflow, improving efficiency and resource utilization. It minimizes material waste by optimizing cutting paths and automatically adjusting machining settings based on real-time data feedback. This feature not only enhances sustainability but also ensures cost-effectiveness for businesses.VIII. Unparalleled Customer Support:The reputable company behind the CNC Turning Center Machine is committed to providing exceptional customer support. Their team of experienced technicians and engineers offers comprehensive training, installation assistance, and ongoing technical support. This dedication ensures that customers can maximize the benefits of the machine and overcome any challenges they may encounter.IX. Conclusion:In an ever-evolving manufacturing landscape, the introduction of the CNC Turning Center Machine signifies a breakthrough in industrial manufacturing. Its precision, advanced features, versatility, and automation capabilities redefine industry standards. The company's commitment to safety, streamlined workflow, and customer support further solidify its position as an industry leader. With this revolutionary machine, manufacturers can embrace a new era of efficiency, accuracy, and productivity.
Unlocking Precision and Efficiency: A Guide to 4 Axis CNC Vertical Milling Machines
Title: Advanced 4-Axis CNC Vertical Milling Machine Unveiled by Prominent ManufacturerIntroduction:In an industry where precision and efficiency are paramount, a leading manufacturer has launched a groundbreaking 4-axis CNC vertical milling machine. With an unwavering commitment to innovation and cutting-edge technology, this new addition promises to revolutionize the manufacturing sector by delivering unparalleled accuracy, versatility, and productivity. With a list of impressive features, the machine is set to redefine manufacturing capabilities across various industries.Precision Engineering and State-of-the-Art Design:The company's dedicated team of engineers has meticulously developed this 4-axis CNC vertical milling machine using state-of-the-art technology. The machine's innovative design ensures the highest levels of precision, enabling users to achieve intricate and complex machining tasks with ease. Equipped with advanced linear guide rails, servomotors, and a rugged C-frame structure, this cutting-edge milling machine guarantees stability, reliability, and enhanced control.Superior Functionality and Enhanced Work Efficiency:The 4-axis CNC vertical milling machine boasts an extensive range of advanced functionalities tailored to meet the diverse needs of manufacturers. With its user-friendly interface and intuitive controls, operators can quickly master the machine's operations, drastically reducing setup time and minimizing the chance for error. Moreover, the machine facilitates seamless transition between different manufacturing processes, providing users with unprecedented flexibility.Unmatched Precision and Versatility:Through the integration of precise digital control systems, this milling machine offers exceptional accuracy and repeatability. With four-axis simultaneous control, manufacturers can effortlessly perform intricate operations such as contouring, engraving, and chamfering. The machine's advanced spindle technology ensures both high-speed and high-torque operations, enabling a wide range of cutting tasks on various materials, including metals, plastics, and composites.Customizable Features and Modular Design:Recognizing the need for adaptability in today's manufacturing environment, the modular design of this 4-axis CNC milling machine allows for flexibility and customization. Manufacturers can select from a range of optional accessories to tailor the machine to their specific requirements. Additionally, the machine's expandable tool magazine accommodates an extensive selection of cutting tools, significantly boosting productivity and reducing downtime.Remote Monitoring and Future-Proof Connectivity:The manufacturer has taken a step ahead in embracing industry 4.0 principles by incorporating remote monitoring and connectivity features into its cutting-edge milling machine. Through an integrated network connection, manufacturers can monitor and control operations from anywhere, enhancing productivity and reducing downtime. Furthermore, the machine's compatibility with CAD/CAM software ensures seamless integration into advanced production workflows, offering abundant opportunities for automation and optimization.Advanced Safety Features and Ergonomic Design:Safety remains a top priority in the manufacturing industry, and this 4-axis CNC vertical milling machine excels in providing a secure working environment. Equipped with advanced sensors and emergency stop buttons, the machine can detect issues promptly, guaranteeing operator safety. Meanwhile, the ergonomic design minimizes operator fatigue by providing an adjustable worktable and convenient access to the control panel, further enhancing productivity and user comfort.Conclusion:Incorporating cutting-edge technology and innovative design, the 4-axis CNC vertical milling machine introduced by this prominent manufacturer is set to redefine the manufacturing landscape. With its unmatched precision, versatility, and efficiency, manufacturers across various industries can now achieve optimized production processes and superior product quality. As the industry progresses into the era of industry 4.0, this new milling machine represents an essential tool for manufacturers seeking improved performance and a competitive edge.
Guide to Manual Knee Mills for Precision Machining: Key Features and Benefits Explored
Title: Manual Knee Mills Market Experiences Remarkable Surge, Indicating Steady Industry GrowthIntroduction:In recent years, the global manufacturing industry has witnessed a resurgence driven by technological advancements and the growing demand for precision machining solutions. Manual Knee Mills (referred to as MKMs), a crucial component of the manufacturing process, have emerged as a sought-after tool due to their versatility and ability to achieve high precision. With several prominent companies operating in this space, the MKM market has experienced a remarkable surge, indicating steady industry growth.I. Overview of the MKM MarketA. Definition and Functionality of MKMs - MKMs are versatile milling machines widely used in manufacturing industries. - Their primary function is to remove material from a workpiece using rotary cutters. - MKMs are manually operated, making them ideal for small-scale operations and precision milling tasks.B. Market Dynamics 1. Technological Advancements Driving Market Growth - Introduction of advanced features, such as digital control systems and enhanced automation, boosts the market demand. - Integration of software solutions for precise and seamless operations. 2. Rising Demand for Precision Machining Solutions - Increasing demand for intricate and complex components in industries like aerospace, automotive, and electronics. - MKMs offer the required precision and accuracy for critical manufacturing operations. 3. Expanding Manufacturing Sector in Developing Economies - Rapid industrialization and infrastructure development in emerging economies drive the market growth. - Growing investments in the manufacturing sector bolster the demand for MKMs.II. Key Players in the MKM MarketA. Company A (name removed) - A leading manufacturer of MKMs with a strong global presence. - Wide range of MKMs catering to diverse industrial requirements. - Strive for continuous innovation to provide cutting-edge solutions.B. Company B (name removed) - Known for its high-quality MKMs and excellent customer service. - Focus on precision and reliability, ensuring customer satisfaction. - Strong dealer network, expanding market reach globally.C. Company C (name removed) - Offers technologically advanced MKMs, incorporating the latest features. - Emphasis on ergonomic designs and operator safety. - Commitment to sustainability, employing energy-efficient manufacturing processes.III. Market Trends and OpportunitiesA. Growing Adoption of CNC-Enabled MKMs - Computer Numerical Control (CNC) integration enhances efficiency and productivity. - Rising demand for automation and reduced manual intervention fuels the adoption.B. Shift Towards Hybrid Machining Solutions - Integration of additive manufacturing techniques with milling processes. - Provides flexibility in achieving complex geometries and reduces production time.C. Rising Demand for Customized MKMs - Manufacturers require specialized MKMs to cater to unique manufacturing needs. - Companies capitalizing on this trend by offering tailor-made solutions.IV. Regional AnalysisA. North America - Robust manufacturing sector supported by technological advancements. - Strong market presence of key players, driving the overall growth.B. Europe - Growing demand for precision machining in aerospace and automotive sectors. - Increasing focus on sustainable and eco-friendly manufacturing methods.C. Asia Pacific - Rapid industrialization and infrastructure development propel the market growth. - Rising investments in the manufacturing sector, especially in China and India.V. ConclusionThe MKM market is experiencing a remarkable surge, backed by technological advancements, increasing demand for precision machining solutions, and the expanding manufacturing sector in developing economies. Key players, such as Company A, Company B, and Company C, are actively driving the market by offering innovative products and excellent customer service. As the adoption of CNC-enabled MKMs and hybrid machining solutions grows, opportunities for customized MKMs are also on the rise. The regional analysis highlights the strong market presence in North America, Europe, and Asia Pacific. With continuous advancements and market demand, the future of the MKM industry looks promising, and it is expected to flourish further in the coming years.
Exploring the Advantages of a Rotary Table Horizontal Boring Mill
Title: Innovative Horizontal Boring Mill with Rotary Table Enhances Precision and EfficiencyIntroduction:In today's ever-evolving landscape of manufacturing and industrial solutions, companies are continuously seeking innovative machinery that maximizes precision, efficiency, and productivity. Addressing these demands, an industry-leading company has introduced its highly advanced Horizontal Boring Mill with Rotary Table—an engineering marvel that redefines machining capabilities and sets new standards for the manufacturing sector.Context:The Horizontal Boring Mill with Rotary Table, developed by an industry pioneer, represents a significant breakthrough in machining technology. With its cutting-edge features and wide-ranging applications, this state-of-the-art equipment promises to revolutionize various sectors, including aerospace, automotive, energy, and beyond.Main Body:1. Precision Engineering at its Finest: The Horizontal Boring Mill with Rotary Table stands out for its exceptional precision and accuracy. Equipped with advanced CNC controls and integrated measurement systems, this revolutionary machine ensures that every component passes the most stringent quality standards. Its meticulous drilling, milling, and boring capabilities guarantee optimal fit and tolerance, resulting in superior end products.2. Advanced Features Enhancing Efficiency:The incorporation of innovative features in the Horizontal Boring Mill with Rotary Table translates into enhanced productivity and efficiency for industrial operations. Equipped with a robust rotary table, a wide range of multi-axis machining operations can be accomplished in a single setup, reducing production time and maximizing output. The machine's high-speed spindle motor enables rapid cutting while maintaining accuracy, further improving efficiency.3. Versatile Applications:With its adaptability and versatility, the Horizontal Boring Mill with Rotary Table caters to a variety of manufacturing needs. From producing complex components for the aerospace industry to manufacturing large-scale automotive parts, this machine is designed to handle a diverse range of projects effectively. Furthermore, its ability to accommodate different materials, including steel, aluminum, and composites, grants companies unmatched flexibility.4. Safety and Ergonomics:While pushing the boundaries of machining capabilities, the Horizontal Boring Mill with Rotary Table also prioritizes operator safety. Incorporating state-of-the-art safety systems ensures a secure working environment for the machine's operators, mitigating risks associated with high-speed rotations and heavy material handling. Additionally, ergonomic design elements, such as easy access to controls and adjustable working positions, reduce operator fatigue and maximize efficiency.5. Cost-Effective Solution:Investing in the Horizontal Boring Mill with Rotary Table translates into long-term cost savings for manufacturing companies. Its unparalleled precision minimizes material wastage and reduces the need for rework, saving valuable resources and improving profitability. Moreover, the machine's enhanced production capabilities accelerate project completion, helping businesses fulfill customer demands while maintaining a competitive edge.Conclusion:The introduction of the Horizontal Boring Mill with Rotary Table marks a significant milestone in the field of precision engineering and machining. With its advanced features, versatile applications, and commitment to safety, this groundbreaking machine promises to be a game-changer for manufacturing industries worldwide. By maximizing efficiency, precision, and productivity, it embraces the future of manufacturing, setting new benchmarks in the quest for excellence.
Exploring the Uses and Advantages of Vertical and Horizontal CNC Milling Machines
Title: Innovative Vertical and Horizontal CNC Milling Machine Revolutionizes Manufacturing ProcessesIntroduction:The manufacturing industry is witnessing a groundbreaking advancement with the introduction of the latest Vertical and Horizontal CNC Milling Machine, developed by a pioneering company in the field. This state-of-the-art machine is set to revolutionize the way manufacturers approach production, delivering exceptional precision, efficiency, and flexibility. By incorporating cutting-edge technology and a user-friendly interface, this innovative milling machine aims to streamline manufacturing processes and maximize productivity like never before.Innovative Features:The Vertical and Horizontal CNC Milling Machine is equipped with a range of innovative features that differentiate it from traditional milling machines. First and foremost, the machine offers high versatility with its ability to perform both vertical and horizontal milling operations. Manufacturers can seamlessly switch between the two modes, allowing for enhanced flexibility in diverse production scenarios.Moreover, the CNC (Computer Numeric Control) technology integrated into the machine enables precise and automated machining processes. Gone are the days of manual adjustment and errors. The advanced control system allows engineers and operators to program and replicate complex designs with ease, ensuring consistent and accurate manufacturing outcomes.The machine's design focuses on improving operational efficiency and reducing setup time. The automatic tool changing system enables swift transitions between different cutters, reducing downtime and enhancing overall productivity. Additionally, the inclusion of a high-speed spindle and efficient coolant system guarantees superior surface finishes and extended tool life, resulting in significant cost savings for manufacturers.Application and Impact:The Vertical and Horizontal CNC Milling Machine caters to a wide range of industries, including automotive, aerospace, electronics, and general manufacturing. Its ability to handle intricate machining tasks makes it an ideal solution for creating complex components, molds, and prototypes. With the increasing demand for precision engineering, this machine promises to elevate the standards of manufacturing excellence and drive industry innovation.Beyond its contribution to the manufacturing sector, the introduction of this advanced milling machine holds great significance in terms of economic growth and competitiveness. By automating processes and reducing human error, manufacturers can significantly improve their production capacities while maintaining high-quality standards. The enhanced efficiency resulting from this machine will enable companies to meet customer demands more efficiently and achieve quicker turnaround times.Company Background and Vision:The development of this revolutionary milling machine can be attributed to {}, a pioneering company in the field. Known for their relentless commitment to technological advancements, {} has been at the forefront of precision machining solutions for over two decades. With a team of experienced engineers and cutting-edge manufacturing facilities, they continue to drive industry innovation and transform the landscape of manufacturing.{} envisions empowering manufacturers worldwide by delivering cutting-edge machinery that surpasses industry standards. Their dedication to continuous research and development ensures that their products are always equipped with the latest technological advancements. By collaborating with clients and understanding their unique requirements, {} ensures that their machines align perfectly with the evolving needs of the manufacturing industry.Conclusion:The introduction of the Vertical and Horizontal CNC Milling Machine signifies a significant leap in manufacturing technology. With its innovative features, advanced CNC control system, and commitment to superior engineering, this machine promises to redefine manufacturing norms and elevate productivity to new heights. As the manufacturing industry embraces automation and precision, {} and their groundbreaking milling machine play an instrumental role in shaping the future of manufacturing processes.
Advanced CNC Knee Milling Cutter Revolutionizes Machining Processes
Title: Revolutionary CNC Knee Milling Cutter Revolutionizes Precision ManufacturingIntroduction:In the ever-advancing world of precision manufacturing, cutting-edge technologies continue to drive innovation and efficiency. One such breakthrough is the development of the CNC Knee Milling Cutter, an exceptional tool that has revolutionized the industry. This state-of-the-art machine, manufactured by a renowned company known for its commitment to excellence and technological advancements, represents a significant leap forward in precision engineering. With its exceptional capabilities and advanced features, it provides manufacturers with an unparalleled level of precision and productivity. In this article, we will delve into the unique characteristics and benefits of the CNC Knee Milling Cutter, highlighting the immense impact it has on the manufacturing landscape.Versatile and Efficient:The CNC Knee Milling Cutter has quickly earned a reputation for its versatility and efficiency. With its advanced computer numerical control (CNC) technology, it offers an expansive range of milling operations, including face milling, end milling, and drilling. This multi-functional approach allows manufacturers to achieve precise results across various materials and components. Moreover, its exceptional speed and accuracy improve overall production efficiency, reducing downtime and enhancing productivity.Unmatched Precision:At the heart of the CNC Knee Milling Cutter lies its unparalleled precision. Equipped with cutting-edge sensors and feedback mechanisms, it ensures meticulous control over cutting depth, optimal tool engagement, and spindle speed. The machine's integrated probing system further enhances precision by automatically measuring workpieces and adjusting toolpaths accordingly. Whether handling large-scale projects or intricate and delicate parts, the CNC Knee Milling Cutter delivers extraordinary precision, minimizing errors and contributing to superior quality outcomes.Enhanced Safety Features:Recognizing the inherent risks associated with large-scale machinery, the company has prioritized safety in the CNC Knee Milling Cutter's design. Equipped with advanced safety features, such as the automatic tool retract system, emergency stop buttons, and comprehensive safety interlocks, operators can work confidently, knowing that their well-being is safeguarded. By implementing these safety measures, the company ensures a secure working environment, reducing the possibility of accidents or injuries.Intuitive Software Interface:As technology continues to advance, ease of use and intuitive control become even more crucial. The CNC Knee Milling Cutter includes a user-friendly software interface that enables operators to program and operate the machine effortlessly. With its intuitive layout and customizable options, even inexperienced users can quickly adapt to the system and achieve optimal results. The software allows for seamless integration with existing manufacturing software, streamlining the workflow and maximizing overall efficiency.Sustainability and Cost-effectiveness:Environmental consciousness is a crucial consideration for modern manufacturing. The CNC Knee Milling Cutter incorporates sustainability features designed to minimize energy consumption and reduce waste. The machine's precision and accuracy also contribute to minimizing material waste, lowering manufacturing costs over time. With its long lifespan and low maintenance requirements, the CNC Knee Milling Cutter provides an excellent return on investment, making it an ideal choice for manufacturing facilities of all sizes.Advancing the Manufacturing Landscape:The CNC Knee Milling Cutter, developed by [Company Name], has proven to be a game-changer in the field of precision manufacturing. Its versatility, precision, and user-friendly interface empower manufacturers to enhance productivity, improve quality, and reduce operational costs. The company's commitment to innovation and its dedication to customer satisfaction have undoubtedly elevated the CNC Knee Milling Cutter to the forefront of the industry. As manufacturers worldwide embrace this revolutionary technology, the future of precision manufacturing appears brighter than ever before.Conclusion:The introduction of the CNC Knee Milling Cutter showcases the relentless pursuit of excellence and innovation in the precision manufacturing sector. Its unmatched precision, versatility, and intuitive design revolutionize the manufacturing process, enabling manufacturers to produce high-quality components with exceptional efficiency. As [Company Name] continues to push the boundaries of technological advancement, one can only anticipate more revolutionary breakthroughs in precision manufacturing.
Revolutionary Vertical Machining Center Takes Manufacturing to New Heights: Discover Advanced Capabilities
Title: Innovative Vertical Machining Center Revolutionizes Manufacturing EfficiencyIntroduction:In today's rapidly advancing technological landscape, vertical machining centers (VMCs) have emerged as essential tools for the manufacturing industry. They enable precision, speed, and efficiency in a variety of machining operations, ranging from milling and drilling to cutting and shaping metal components. One such groundbreaking VMC has gained significant attention due to its innovative features and exceptional performance capabilities.Enhancing Manufacturing Efficiency:The revolutionary VMC, developed by a leading engineering company, is designed to optimize manufacturing processes and decrease production timelines, ultimately improving overall efficiency. Employing state-of-the-art technology and cutting-edge automation, this VMC streamlines operations and reduces human error, leading to enhanced productivity.Enhanced Accuracy and Precision:The VMC boasts superior accuracy and precision, enabling manufacturers to achieve exceptional results in a wide range of applications. Equipped with advanced computer numerical control (CNC) systems, this machining center guarantees precise movement control, resulting in consistently high-quality finished products. Its robust structural design and rigidity contribute to minimizing vibrations, ensuring optimal stability during the machining process.Customization and Adaptability:In response to the demands of a rapidly evolving manufacturing industry, this VMC provides exceptional customization and adaptability features. It allows operators to adapt the machining center to fit the specific needs of a particular project, ensuring a perfect match between the requirements and the machining parameters. With user-friendly software interfaces and intuitive control systems, the VMC enables operators to make adjustments efficiently, reducing downtime and increasing overall efficiency.Optimized Spindle Performance:The VMC's spindle system plays a crucial role in determining machining efficiency. With a powerful spindle motor and sophisticated cooling mechanisms, this VMC ensures a stable and consistent material removal rate, resulting in faster machining while maintaining accuracy. The advanced cooling system also prevents the spindle from overheating, increasing its longevity and minimizing potential downtime due to maintenance requirements.Automation and Smart Features:Equipped with advanced automation capabilities, this VMC reduces reliance on manual involvement, eliminating human error and increasing productivity. The integration of robotic arms and intelligent material handling systems ensures seamless material loading and unloading, minimizing cycle times. Additionally, real-time monitoring and data analysis capabilities enable operators to identify and rectify bottlenecks swiftly, further optimizing production processes.Energy Efficiency:Recognizing the growing importance of sustainable manufacturing, this VMC incorporates energy-efficient components and processes. Leveraging advanced technologies, such as regenerative braking systems and power management modules, the VMC reduces power consumption and significantly lowers the overall carbon footprint. This eco-friendly approach aligns with the company's commitment to environmental responsibility and sustainable manufacturing practices.Future Outlook:As the manufacturing industry continues to evolve, the need for efficient, precise, and adaptable machining centers becomes increasingly crucial. This innovative VMC sets a new benchmark for manufacturing efficiency, providing an array of cutting-edge features designed to meet the evolving demands of the industry. With its exceptional performance, accuracy, and green initiatives, this VMC is poised to transform the manufacturing landscape and empower businesses to thrive in a highly competitive marketplace.Conclusion:The introduction of this groundbreaking VMC unveils new possibilities for manufacturers worldwide. By incorporating advanced technologies, customization options, and automation capabilities, this machining center redefines efficiency, precision, and sustainability in the manufacturing sector. As industries continue to seek the highest standards of quality and productivity, the innovative VMC undoubtedly positions itself as a game-changer.
Ultimate Guide to Manual Knee Mills: Everything You Need to Know
Title: Revolutionary Manual Knee Mills Introduced by Leading Manufacturing Company Introduction:Leading manufacturing company, XYZ Industries (name removed), is proud to announce the launch of their highly anticipated Manual Knee Mills, designed to revolutionize the milling industry. With their cutting-edge technology, advanced features, and unmatched precision, these mills are set to redefine machining capabilities. XYZ Industries aims to provide engineers and machinists with the tools they need to achieve their manufacturing goals efficiently and effectively. I. Features and Benefits:XYZ Industries' Manual Knee Mills offer a wide range of advanced features that cater to the evolving needs of the machining industry. Some key benefits of these mills include:1. Precision Engineering: The Manual Knee Mills incorporate state-of-the-art technology, allowing for exceptional precision and accuracy in the milling process. This precision is crucial for industries such as aerospace, automotive, and medical device manufacturing.2. Versatility: These mills are designed to handle a variety of materials, from soft metals to hardened steel, enabling engineers to perform a wide array of milling tasks with ease.3. User-Friendly Interface: XYZ Industries understands the importance of user experience. The Manual Knee Mills feature an intuitive interface that ensures operators can efficiently navigate through the machine's functions, reducing human error and enhancing productivity.4. Enhanced Visibility: The mills are equipped with LED lighting systems that provide optimal visibility, even in low-light conditions. This feature guarantees better control and precision during the milling process.5. Durability and Reliability: XYZ Industries ensures that their machines are manufactured using high-quality materials, making them robust and long-lasting. These mills are built to withstand the rigors of demanding machining operations.II. Cutting-Edge Technology:XYZ Industries has always been at the forefront of technological advancements in the manufacturing industry. The Manual Knee Mills reflect their commitment to innovation and utilizing the latest technologies. The following technologies are incorporated into these mills:1. Digital Readout (DRO) Systems: The mills are equipped with DRO systems, which provide real-time feedback on the machine's position, allowing operators to make precise adjustments quickly.2. Variable Speed Control: The mills offer variable speed control, allowing engineers to adapt the milling process according to the specific material being machined. This flexibility ensures optimal results and reduced machining time.3. Ergonomic Design: XYZ Industries prioritizes both functionality and user comfort. The Manual Knee Mills feature an ergonomic design with adjustable handles and controls, enabling operators to work in a comfortable and efficient manner.III. Industry Impact:XYZ Industries' Manual Knee Mills are expected to create a significant impact on the machining industry, for several reasons:1. Improved Productivity: The precision and user-friendly features of these mills increase productivity, reducing milling time and minimizing errors. This translates into faster production cycles and improved overall efficiency.2. Cost-Effectiveness: The mills offer an exceptional price-performance ratio, making them a cost-effective solution for machinists and manufacturers. The advanced features and versatility of these mills eliminate the need for additional equipment, providing significant cost savings.3. Advancement of Manufacturing Standards: The introduction of these mills raises the bar in terms of milling precision, consistency, and reliability. As a result, other manufacturers will be compelled to enhance their offerings to remain competitive in the market.In conclusion, XYZ Industries' release of their revolutionary Manual Knee Mills signifies a significant milestone in the manufacturing industry. These versatile tools with their advanced features and cutting-edge technology are set to transform machining capabilities. With unparalleled precision and user-friendly interfaces, engineers and machinists can look forward to increased productivity, improved cost-effectiveness, and the ability to achieve their manufacturing goals with utmost precision. XYZ Industries continues to spearhead innovation, pushing boundaries, and setting new standards in the machining industry.
Exploring the Advantages of Horizontal Machining Centers in Industrial Settings
Title: Advancements in Horizontal Machining Centers Revolutionize Precision Manufacturing Introduction:With continuous advancements in technology, the manufacturing industry has witnessed a significant evolution in machining processes. Horizontal Machining Centers (HMCs), known for their high precision and efficiency, have played a crucial role in transforming contemporary manufacturing practices. This article explores the latest innovations in HMC technology and their contributions to precision manufacturing.1. Efficiency and Precision Redefined:HMCs have redefined the concept of efficiency and precision in modern manufacturing. Equipped with multiple cutting tools, these machines can simultaneously execute multiple operations, minimizing production time and increasing productivity. Their horizontal spindle orientation enables better chip evacuation, resulting in smoother and cleaner finishes. The technological advancements in HMCs have facilitated the production of complex components with impeccable accuracy, fulfilling the demands of today's industries.2. Integrated Automation and Robotics:To further enhance productivity and reduce manual labor, HMCs are now being integrated with advanced automation and robotic systems. The latest HMC models incorporate robotic loading and unloading systems, eliminating the need for human intervention and maximizing uptime. These automated solutions ensure continuous operation and reduce the risk of errors, ultimately enhancing the overall manufacturing process.3. Intelligent Control Systems:Intelligent control systems have revolutionized HMC operations, offering real-time monitoring and optimization of machining processes. The integration of Internet of Things (IoT) technology enables HMCs to connect with other machines, sensors, and data collection systems, facilitating data-driven decision-making. This connectivity allows manufacturers to gather valuable insights, thus optimizing production and minimizing downtime.4. Advanced Tooling Technology:The development of advanced tooling technology has greatly contributed to the efficiency and effectiveness of HMCs. Innovative cutting tools, such as multi-axis milling heads and high-speed machining spindles, enable HMCs to perform a wide range of operations with precision and versatility. Furthermore, the integration of tool pre-setters and tool life monitoring systems ensures efficient tool management, minimizing tool wear and reducing costs.5. Focus on Energy Efficiency:With sustainability gaining traction in the manufacturing industry, HMC manufacturers are increasingly focusing on energy-efficient solutions. The latest HMC models incorporate energy-saving features, such as regenerative braking systems and intelligent power management, reducing the overall energy consumption. These eco-friendly advancements not only contribute to a greener future but also offer cost savings for manufacturers.6. Enhanced Software Capabilities:The software capabilities of HMCs have evolved significantly, providing manufacturers with intuitive interfaces and advanced programming features. Programming languages such as CAD/CAM and G-code simplify the creation of complex machining operations. Additionally, simulation software allows manufacturers to validate programs and identify potential issues before execution, reducing errors and optimizing production.7. Industry-Specific Applications:HMCs find applications in various industries, including aerospace, automotive, and medical. The versatility of HMCs allows for the machining of large and heavy-duty parts, making them suitable for industries that require robust and precise components. Their ability to handle multiple operations simultaneously ensures faster turnaround times and reliable production processes, meeting the specific demands of each industry.Conclusion:Horizontal Machining Centers have undoubtedly transformed the precision manufacturing landscape. The combination of advanced technology and innovative features has revolutionized the efficiency, accuracy, and productivity of modern machining operations. With further advancements on the horizon, HMCs are poised to play a vital role in pushing the boundaries of precision manufacturing in the years to come.
Advanced CNC Mill Turn Center: Revolutionizing Machining Efficiency and Precision
[Assistant]I apologize, but I cannot provide a specific news article as per your request. However, I can help you with a general template to write a news article of approximately 800 words about CNC mill-turn centers and their applications. Please find the template below.[Title]Advancements in CNC Mill-Turn Centers Revolutionize the Manufacturing Industry[Subheading]Introducing the Seamless Blending of Precision Turning and Milling Processes[Publication Date][City], [State] - The manufacturing industry continues to see significant improvements in efficiency and precision, thanks to the latest advancements in Computer Numerical Control (CNC) technology. One such breakthrough is the development of CNC mill-turn centers, designed to seamlessly combine precision turning and milling processes into a single machine. This revolutionary technology, which has already started to reshape the industry landscape, is set to bring unprecedented levels of speed, accuracy, and versatility to manufacturers worldwide.[CNC Mill-Turn Center Brand] (Remove brand name) is one of the pioneering companies at the forefront of this breakthrough. With a strong commitment to innovation and customer satisfaction, they have introduced a state-of-the-art CNC mill-turn center that is revolutionizing manufacturing processes across various sectors. By merging traditional turning and milling functionalities into a single machine, this cutting-edge technology provides manufacturers with a dynamic solution that enhances productivity and reduces production time.The unique capabilities of the CNC mill-turn centers enable manufacturers to carry out complex machining operations with utmost precision. The combination of turning and milling functions in one machine eliminates the need for multiple setups, tool changes, and manual interventions, thereby significantly reducing production costs and improving overall productivity. This technology also facilitates enhanced geometric dimensioning and tolerancing (GD&T), ensuring the highest level of accuracy and reproducibility in component manufacturing.One of the primary advantages of CNC mill-turn centers is their ability to perform simultaneous, multi-axis machining operations. Whether it's turning, drilling, milling, or even grinding, this all-in-one machine can effortlessly carry out these processes in rapid succession, resulting in reduced lead times and increased throughput. This level of flexibility allows manufacturers to meet the ever-growing demands of customers, who often require intricate, high-precision components in limited timeframes.Another crucial aspect that sets CNC mill-turn centers apart is their compatibility with a wide range of materials. Whether it's metals, alloys, composites, or plastics, these versatile machines can handle various materials with ease. This adaptability is particularly valuable in industries such as aerospace, automotive, and medical, where diverse materials are used for complex components. By streamlining the machining process, CNC mill-turn centers offer manufacturers an edge in delivering high-quality products while maintaining cost-effectiveness.The integration of advanced automation and robotic systems further enhances the capabilities of CNC mill-turn centers. With the ability to automate tool changes, material handling, and part positioning, manufacturers can achieve higher efficiency and reduce the need for manual labor. Additionally, built-in sensors and real-time monitoring systems enable manufacturers to maintain optimal machine performance and identify potential issues before they lead to costly downtime.In conclusion, CNC mill-turn centers represent a significant leap forward in the manufacturing industry. By integrating turning and milling operations into a single machine, manufacturers can enjoy enhanced productivity, increased efficiency, and improved product quality. With a commitment to pushing the boundaries of CNC technology, [CNC Mill-Turn Center Brand] (Remove brand name) is playing a vital role in advancing the manufacturing industry and helping businesses thrive in an increasingly competitive market.